磁場位置感測器的動態誤差問題有解。新一代磁性位置感測器,由於導入了專利的動態角度誤差補償技術,因而可克服傳播延遲造成的誤差,將有助馬達系統的轉矩與效率達到最大化。
現今馬達有許多方法可感測位置。如光學編碼器長久以來便受到馬達控制器設計人員青睞,因為它們不僅有高精準度,標準的「ABI」輸出,也能被現在的微處理器(MPU)簡單運用。
不過,由於磁性位置感測器體積很小,且不受灰塵、油脂與溼氣汙染,如今比較常採用非接觸式磁性位置感測器,因此採用磁性位置感測器能幫助應用裝置控制尺寸與穩定度等重要的特質。
但過去的一股潮流阻礙磁性位置感測器的發展--新的無刷直流(Brushless DC, BLDC)馬達通常把提高效率以降低功耗作為目標。同時,設計人員致力於增加新發動機的轉矩,達到低速運轉以支援直接驅動系統,並可免除齒輪箱的必要,進而大幅降低物料(BOM)成本。
為使轉矩與效率達到最大值,無刷直流馬達須要在高速旋轉下,精準地測量轉子旋轉角度,但過去傳統磁性位置感測器很難做到這一點。不過,目前感測器設計已有所突破,新一代裝置不僅能在高速下達到近乎完美的角度測量,也已可進行量產。
整合半導體/霍爾感測器 磁性編碼器提供精準角度
無刷直流馬達由一個旋轉永久磁鐵(Rotating Permanent Magnet)(轉子)與三個或以上相同間距的固定線圈(Spaced Fixed Winding)(定子)組成。藉由控制定子線圈內的電流,可製造一個任意方向與大小的磁場。轉子與定子磁場在轉軸上的相吸/相斥作用,即產生轉矩。
轉矩可在定子磁場垂直於轉子磁場時達到最大。所述轉子的角位移測量提供反饋給控制流經定子繞組(圖1)的電流,以產生正交磁場。藉由測量轉子的角位移,能提供反饋給控制定子線圈電流的系統,進而製造垂直的磁場。
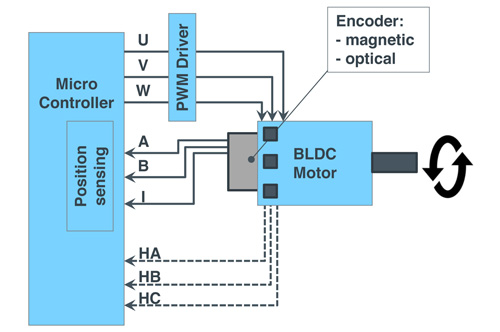 |
圖1 無刷直流馬達控制系統需要使用轉子的角位移的測量結果,來建立一套閉鎖反饋迴路,此測量能由磁性位置感測器(通常用於汽車應用)或光位置感測器(通常用於工業應用)進行。 |
在最先進的應用中,無刷直流馬達會被永磁同步馬達(Permanent Magnet Synchronous Motor, PMSM)取代。永磁同步馬達取代無刷直流馬達內的區塊轉換方案(Block Commutation Scheme),改善轉矩脈動的問題,並能平滑地在線圈間切換,進而減少震動並提升效率。
當然,工業與汽車馬達設計必須經常優化效率、穩定度;其他的馬達特別是消費性產品類型的,則最著重於成本。對於簡單的馬達,一系列霍爾開關提供適當的位置測量方法,能產生足夠的轉矩與平滑度,但是霍爾開關陣列的精密度與準確度,難以滿足高效能馬達對於轉矩與效率的需求。
相比之下,磁性編碼器將一個半導體與霍爾感測器整合在晶粒中,能產生精密、高解析度的定位數據,在轉子靜止或低速轉動時提供高精準度。況且,不同於工業應用中常見的光學編碼器,磁性位置感測器不受汙染影響,且占用空間小。
但除此之外,大多數霍爾感測積體電路(IC)有兩項重大缺點:
這些缺點將增加系統成本與影響性能:要補償動態角度誤差,需要高效能處理能力;而額外的屏蔽可保護IC免受去磁場干擾,但會增加硬體物料成本。
傳播延遲影響動態角度誤差
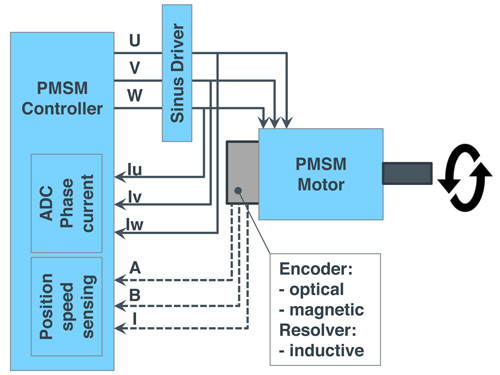 |
圖2 永磁同步馬達也運用類似於無刷直流馬達的反饋迴路。 |
霍爾感測IC對轉子軸上的磁鐵產生的磁場強度進行持續採樣,IC被安裝在固定位置,表面平行於軸上旋轉磁鐵的表面,中間通常間隔一個1~2毫米(mm)的氣隙。此IC包含訊號調節與處理電路,能將磁場強度測量數據,轉換計算成轉子的角位移(單位為度)。執行轉換所需的時間,即為IC固定的傳播延遲(圖3)。不同IC之間的延遲時間也不同,但近日市場上的IC,傳播延遲在10~400微秒(μs)之間不等。
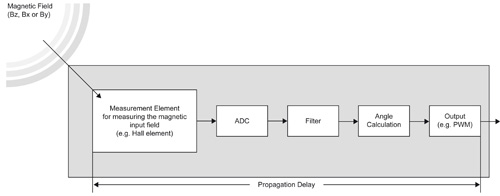 |
圖3 磁性位置感測器的訊號處理造成傳播延遲 |
傳播延遲的問題是,它在轉子轉動時造成動態角度誤差,誤差隨轉速而增加,呈線性關係;傳播延遲與速度越增加,動態角度誤差越大(圖4)。
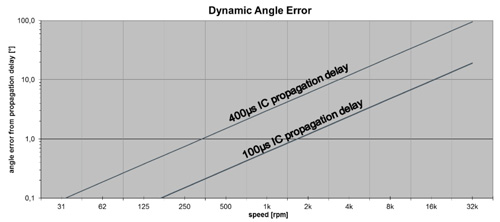 |
圖4 動態誤差與轉速呈線性關係 |
圖5顯示動態誤差的增加情形。假設IC於轉子在A線位置時測量到磁場強度。另假設轉子正在旋轉,而該IC的傳播延遲為100微秒。則等到IC將磁場強度樣本轉換成角度來計算時,轉子就已經轉了100微秒至B線位置,但IC仍會告訴馬達控制引擎控制單元(Engine Control Unit, ECU)或微控制器(MCU):轉子在A線。
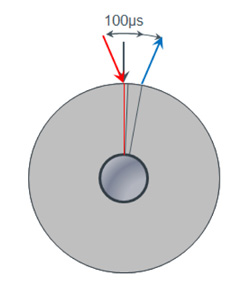 |
圖5 傳播延遲如何使動態角度誤差加劇 |
若沒有補償,通訊方案對定子線圈的優化調整,會是針對A線位置的情形,而非B線位置,這會讓系統無法將轉矩提升至最大,造成浪費能源與系統效率降低。
如果IC的傳播延遲為100微秒且馬達轉速1,000rpm,動態誤差為1.2o;若將轉子速度提升至10,000rpm,則動態角度誤差為12o。
傳播延遲是所有磁性位置感測器的特徵,因此系統設計工程師學會套用補償演算法,試圖減少動態誤差大小。不幸的是,對每秒數以千計的樣本套用補償,會對主機ECU造成巨大負擔,甚至可能需要增加一個專門補償誤差的MCU。
額外的物料成本很不理想,但是把設計團隊的時間用來對補償演算法進行研發、測試與除錯卻也不盡理想。
消除動態角度誤差 新技術具整合補償
如上所述,磁場位置感測器的傳播延遲是固定的,而動態誤差的值,由傳播延遲的持續時間與旋轉速度決定。
現在則有一種全新技術,能將這種補償方案直接植入磁性感測器本身,由感測器業者研發並申請專利中,稱作動態角度誤差補償(Dynamic Angle Error Compensation, DAEC)。在汽車位置感測器中,這種內部補償技術能將傳播延遲降低至1.9微秒,這表示在14,500rpm轉速下,該感測器測量數據衍生的動態誤差僅有0.17o,幾乎可忽略不計。
圖6顯示新型感測器的測量輸出(左圖)與傳統磁性位置感測器輸出(右圖)的不同,以及有精準的光學編碼器輸出供為參考。如右圖,感測器輸出受到200微秒的傳播延遲,在14,500rpm轉速下產生18o的誤差。
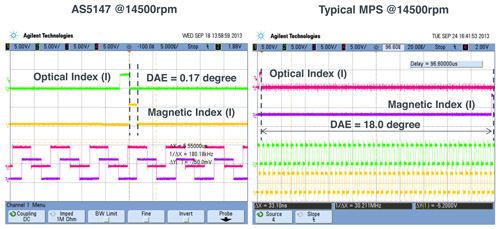 |
圖6 感測器輸出:左側具有整合補償,右側沒有。 |
對比之下,新型感測器的誤差可忽略不計,表示它的訊號不需外部補償,即可直接由整流控制器使用。實際上,DAEC技術提供的內部補償之所以能產生比外部補償還小的動態角度誤差,是因為這些取樣誤差通常是在ECU與MCU上發生的。
當然,感測器的內部補償也能減少系統成本,因為不需要額外的MCU進行誤差補償,或不需要那麼厲害的ECU(圖7)。
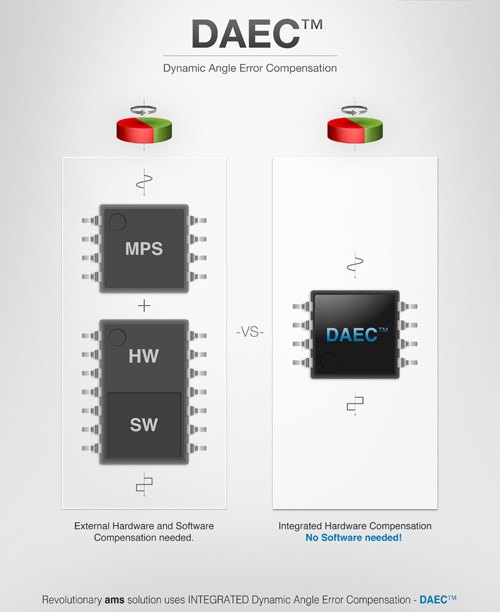 |
圖7 左側顯示傳統的動態角度誤差補償的分立方案;右側是新整合的動態角度誤差補償方法。 |
許多磁性位置感測器的另外一個缺點是,他們對去磁場很敏感。轉子磁場以外的磁場干擾,會隨機竄改許多IC的角度測量,而這類隨機誤差不能由主機ECU或MCU補償。這使得使用者不得不屏蔽IC,但是這樣不僅提高物料成本與裝配成本,也可能因為該應用的空間有限而妥協機械設計。
隨著ISO 26262功能安全標準應用於汽車中,馬達系統內去磁場的抗擾設計也成為強制規定。目前市場上這項獲得專利的「差動感測」技術,能改善所有磁場位置感測器,且抗擾高達25,000A/m的去磁場,不須屏蔽任何強度低於25,000A/m的去磁場。
動態角度誤差補償技術的導入,幫助無刷直流馬達與永磁同步馬達製造業者可以得到極精確的位置數據,減少誤差,進而在高速應用中將轉矩極大化,但同時也能夠享受磁性位置感測器小體積與可靠度的優勢。
DAEC現在可應用在AS5147(單片)與AS5247(雙冗片, Dual Redundant Dies)兩款汽車磁性位置感測器(AEC-Q100零級汽車認證),以支援汽車應用裝置中的無刷直流馬達換能,例如電能輔助動力方向盤(EPS)、傳輸(變速箱、驅動器)、幫浦與煞車。
對於工業應用裝置,DAEC已可用於AS5047D,提供十進位ABI輸出,可理想且相對等(Like-for-like)地取代光學編碼器。
(本文作者為奧地利微電子產品經理)