近兩年的全球行動通訊大會(MWC)各大車廠皆推出車聯網的應用概念,兩大行動裝置作業系統開發商蘋果(Apple)與Google也正式跨足汽車領域,分別發表CarPlay和Android Auto平台。
除了Google無人駕駛車,包含賓士(Benz)、寶馬(BMW)、富豪(Volvo)、一汽集團、中國軍事交通學院等等產官機構都已完成無人駕駛技術開發並開始進行道路實驗,中國大陸的網路企業百度、樂視也在無人駕駛的領域展現積極切入動作。
全球汽車電子的產值將會因為應用平台的成熟而大幅成長。車用IC的在2018前的年複合成長率為10.8%,為更領域之最,其中亞太區的車用IC更高達20%,IC業者無不磨刀霍霍地準備強攻此新藍海市場。
車用IC的市場相較於資通訊科技(ICT)產業的最大差異為市場較為封閉,且前期的開發及驗證期可能長達3年,對台灣、中國大陸IC業者已習慣即時上市(Time to Market)的運作模式相悖,價值理念也不盡相同,本文將說明AEC-Q100的IC驗證規範並解析晶片商如何滿足車廠/模組廠客戶的需求,探討焦點將放在2014年9月新改版規範AEC-Q100 H版的要求進行解讀。
打入車電供應鏈 門檻為AEC和ISO/TS 16949
要進入車輛領域,打入各一級(Tier1)車電大廠供應鏈,必須取得兩張門票,第一張是由北美汽車產業所推的AEC-Q100(IC)、101(離散元件)、200(被動零件)可靠度標準;第二張門票,則要符合零失效(Zero Defect)的供應鏈品質管理標準ISO/TS 16949規範(Quality Management System),其關連性可參考圖1說明。
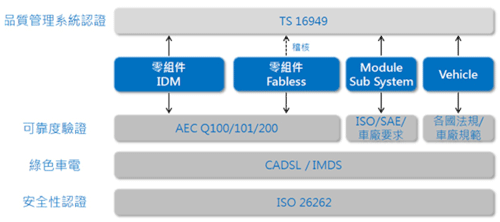 |
圖1 車用零組件基本要求說明圖 |
車用零組件市場差異 左右可靠度品質要求
汽車零組件市場可以大致區分為三部分,包括OEM/ODM(正廠出廠零件)/OES(正廠維修零件)、DOP(Dealer Option經銷商選配零件)、AM(After Marketing副廠零件)。
對客戶的失效率預估及備品備置策略會因決定進入不同市場而有所變化,OEM/ODM/OES為原廠保固,因其保固期較長,各車廠需要在製造及售後服務的成本之間取得平衡,IC供應商要進入的門檻較高。DOP則為各經銷商因在地市場的銷售策略需求所做的選配項目,進入門檻與上述相近,售後市場(AM)與原廠保固無關,所以相對進入門檻和成本較低。另一面向為AM的產品類型較多屬於影音周邊與主被動安全無關,所要求的可靠度也低於原廠零件(圖2)。
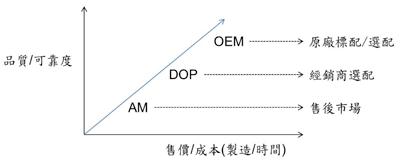 |
圖2 車用零組件市場差異 |
了解車用IC規範AEC-Q100驗證流程
那麼,IC設計業者該如何進入車用IC供應鏈呢?首先應先了解其中的一張門票AEC-Q100。圖3為AEC-Q100規範中的驗證流程,此圖是以Die Design→Wafer Fab.→PKG Assembly→Testing的製造流程來繪製,各群組的關聯性須要參考圖中的箭頭符號,這裡將驗證流程分為五個部分進行簡易說明,各項測試的細節部分就不再細述。
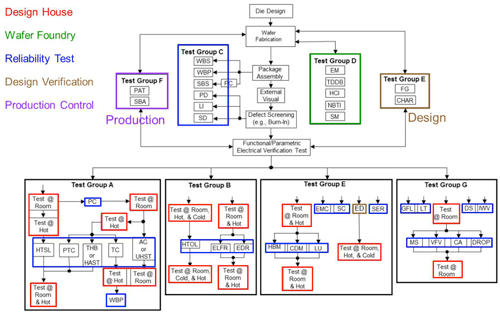 |
圖3 AEC-Q100驗證流程 |
區域1為可靠度實驗前後的功能測試,此部分須要IC設計公司與測試廠討論執行方式,與一般IC驗證主要差異在功能測試的溫度設定,此部分稍後會進行說明。
Group D的區域2為晶圓廠在晶圓級(Wafer Level)的可靠度驗證,無晶圓(Fabless)的IC業須與委託製造的晶圓廠取得相關資料。
區域3為可靠性視產品包裝/特性需要執行的項目,AEC將其分為Group A(加速環境應力實驗)、Group B(加速工作壽命模擬)、Group C(封裝完整性測試)、Group E(電性驗證測試)、Group G(空腔/密封型封裝完整性測試)。
部分Group E的區域4為設計階段的失效模式與影響分析評估,成品階段的特性驗證以及故障涵蓋率計算。
Group F的區域生產階段的品質控管,包含良率/Bin使用統計手法進行控管及制定標準處理流程。
讀解AEC-Q100 H版本新要求
自2007年5月,AEC-Q100 H版發佈後,時隔7年以上的時間,2014年9月,G版發佈,此段內文將探討AEC-Q100 H版與G版之間的主要差異,及改版後規範的說明。
檢視溫度等級
IC供應商必須先了解終端客戶如何使用此IC及其在車內的安裝位置,以實際應用的溫度範圍來訂定合適的溫度等級,此溫度等級定義會應用在兩個部分。
第一部分為測試計畫展開時各可靠度實驗的條件選擇,如溫度循環(Temperature Cycling, TCT)實驗,不同等級的溫變範圍及溫差循環數會有差異。
第二部分為前述的可靠度實驗前後功能性測試溫度必須依照使用者(User)所訂定的溫度範圍來做功能應用的最後測試(Final Test, FT)測試,訂定溫度等級為Grade 1(-40℃∼125℃),則代表FT時使用低溫-40℃、常溫25℃及高溫125℃,且須要留意其測試溫度有先後順序的訂定。如高溫工作壽命(High Temperature Operating Life, HTOL)實驗在FT測試定義順序為Room→Cold→Hot。
新版的部分取消了Grade 4 0℃∼70℃的溫度等級(表1),此溫度等級若比對車用模組在ISO 16750/SAE J1211等規範內的描述是無法對應到合適的產品,因此筆者認為取消此溫度等級是更貼近實際模組的要求。
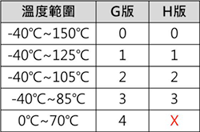 |
表1 Temperature Grade定義 |
比較實驗項目
在新版中,增減項目包括以下所述的兩種。
閘極漏電(Gate Leakage, GL)的部分主要在模擬車用模組應用時所可能遭遇高溫及高電場同時發生的環境,此環境會讓IC封裝(Package)內的等效電容及電阻產生GL的失效,此失效現象可經由高溫烘烤的方式恢復。
取消的原因規範中未有說明,但以多年累積的驗證測試經驗來看,此失效模式常發生在預燒(Burn-In)及迴焊(Reflow)的過程,雖規範已取消,在生產過程或實際應用客退若有相同失效發生,仍可使用此手法進行再現性實驗。
機器模型(Machine Mode, MM)的部分則與JEDEC的JESD47規範同步,一是人體模式(Human Body Model, HBM)可以等效MM的實驗結果,二是元件充電模式(Charged Device Model, CDM),重要性更勝於MM,因此應多著重在CDM的測試。
至於文獻中提到的HBM與MM的關聯性,以實務經驗來看,仍有部分產品的ESD防護電路在HBM和MM上是有所差異的,規範雖然取消此項目,但IC業者仍須要面對當ESD客退發生時的處理,ESD定義為設計驗證,所以目前各家廠商仍將其列為標準測試項目。
車電與醫療產業不同於資通訊科技產業,車電與醫療產業注重的科技是技術成熟性、可靠性以及零失效,而非資通訊科技所追求最先進的技術,因此,車用電子產品在無鉛製程的轉換時程是比消費性產品來得晚,此次正式列入測試項目也代表無鉛製程的轉換已相當成熟,但仍允許部分如引擎室內高溫應用等產品使用有鉛製程。無鉛的驗證項目則包含可焊性(Solderability)、Solder Heat Resistance以及錫鬚(Whisker)。
改變實驗條件
主要實驗條件改變的部分在於高溫工作壽命(HTOL)及溫度循環(TCT)兩項實驗,其餘如打線(Wire Bonding)的相關實驗則是取消Ppk的計算使用Cpk則可、Solderability則說明可由烘烤替代蒸氣老化、Group G部分的實驗樣品數則略為減少,測試項目所參考規範調整的部分請自行參閱,在此不細述。
有三個部分,一為實驗時間增長皆為1,000Hrs,二為清楚定義溫度為連接溫度(Junction Temperature, Tj),三為實驗高溫對齊Grade的定義。
最低標的低溫溫度由-50℃調整為-55℃,Cycle數的部分則有部分提升,仍可參考JESD22-A104的規範進行等效實驗條件的替換。實驗條件的部分可再參考稍後第五部分的說明,將可更理解此次規範變更所要表達含意。
何謂通用性資料
先以圖4來說明通用性資料(Generic Data)的基本含意,A、B兩個產品若使用相同製程或材料,則可初步定義為同一家族系列產品,若對A產品進行完整AEC Q-100 Qualification,相同製程或材料的部分所產出的測試結果則稱之為Generic Data,先不論驗證的數量與程序,只要Generic Data的定義符合AEC-Q100的說明,B產品進行剩餘項目的驗證後再加上Generic Data,則可宣告B產品也通過AEC-Q100。
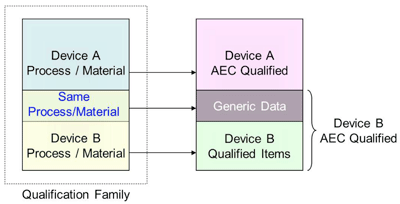 |
圖4 Qualification Family及Generic Data |
此次新的版本對於Generic Data及Qualification Family的定義及使用原則有較清晰的說明,並且簡化其認證程序,同時以情境模擬案例說明哪些製程變更時應進行哪些實驗項目與Lot數量,都有較明確的定義,因內容過多,若有需要可以再參閱規範。
擬定測試計畫
本文中最重要、也是此次改版中變動最大的部分是,呼應美國汽車工程師協會在規範SAE-J1879/J1211中強調的強韌性/穩健性驗證(Robustness Validation),驗證計畫應思考的是,因應該產品在實際應用環境所面臨的使用條件而擬定的,而非以單一測試標準/條件來適用所有產品,也就是應用測試(Test for Application),而非標準測試(Test for Standard)。
當擬定一個合適的驗證計畫時,第一步為制定該元件被設計/生產的目的,稱之為Mission Profile,除了滿足功能性的任務外,要再加上可靠度的任務,表2為汽車的Mission Profile參數範例。
 |
表2 Example of Vehicle Mission Profile |
IC供應商須考量不同應用功能的元件將會對應不同的Mission Profile,若IC工作行為是在非作業時間(Non-Operating Time),如警報器等的應用,則工作時間(Life Time)條件應滿足116,400Hrs在常溫的情況。
若IC僅在Engine On時工作,那Mission Profile就必須要滿足12,000Hrs的壽命時間,及其工作位置的使用溫度,假定Engine On時該IC平均的工作溫度Junction Temperature(Tj)=87℃,使用的HTOL測試溫度為125℃,活化能設定為0.7eV,接下來使用阿累尼亞斯模型(Arrhenius Model)來計算實驗時的溫度加速率,如公式1計算:
AFT=exp(Ea/k)(1/Tuse-1/Tstress)
......................................................公式1
如此即可算出溫度加速率AFT=8.6232,以上述的設定目標壽命為12,000Hrs,因此HTO實驗時間應為12,000Hrs/8.6232=1,392Hrs。
除了溫度加速的範例,包含溫度循環/濕度的加速公式已列在新規範中,可再參考規範內文。
上述範例旨在說明如何以終端產品實際應用的Mission Profile來設計合適的測試計畫,相信很多從事IC設計的品管單位都相當熟悉,本文要表達的是規範將逐漸捨棄以單一標準來訂定,而是交由終端使用者(End User)與零組件製造商(Component Manufacturer)來共同制定合宜的驗證計畫。制定驗證計畫的流程可參閱圖5的說明。
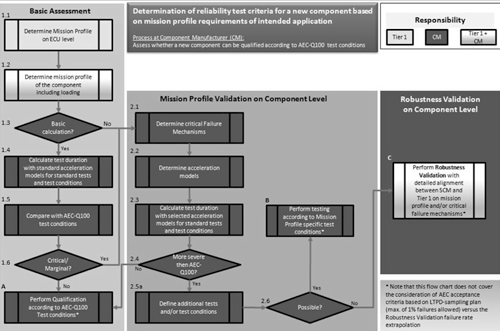 |
圖5 Reliability Test Criteria for New Component |
制定相應驗證步驟 方能打入車廠供應鏈
消費性產品的產品功能設計,一般IC設計業者早已駕輕就熟,而這一兩年,隨著汽車市場逐步走向車聯網、電動車領域,需要更多駕駛資訊輔助整合系統,也讓IC設計業者找到進入市場的敲門磚。然而,消費性電子產品而言,產品壽命設計約1∼3年為汰換週期,但車用電子則以10年起跳,上看15年壽命期。如何尋找有經驗的實驗室,協助客戶了解車規,制定相對應的AEC-Q100驗證步驟與手法,順利進入車廠供應鏈,是極為重要的事。
(本文作者為宜特可靠度工程處處長)