以往編碼器使用者一直不願意改變,因為一些創新技術聲稱具備卓越性能與可靠性,但卻缺乏可追蹤的紀錄和大量過往資料來為其佐證,其實並不適合用於廠區或工業裝置中的馬達控制。
產業中多年來一直使用光學編碼器和磁編碼器,它們採用看似更具體的物理概念,然而電容式編碼器也是建基於經過全面試驗的原理,而且擁有業界多年來的成功實績作為證明。這種運動感測替代方法是數位式的,可提供許多效益,將把利用旋轉換向編碼器(Rotary Commutation Encoder)的設計人員帶到一個全新的智慧等級。
旋轉編碼器對於所有的運動-控制應用來說幾乎都是相當關鍵的,而且由於無刷直流(BLDC)馬達的使用增加,進一步擴大旋轉編碼器的需求,並且帶來控制、精度和效率等方面的諸多效益。編碼器的任務很簡單,原則上就是為系統控制器指出馬達軸(Motor Shaft)的位置(圖1)。控制器利用這種資訊可以準確且有效地對馬達繞組(Motor Winding)進行轉向以及確定速度、方向和加速等參數,運動控制迴路需要這些參數來維持所要求的馬達性能。
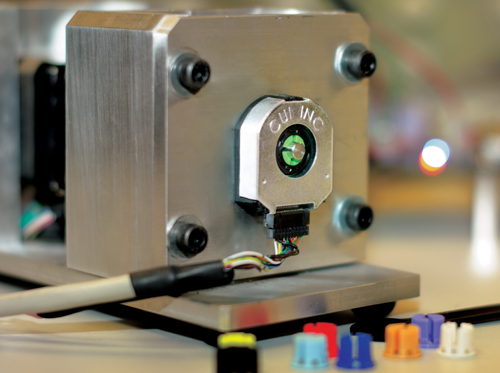 |
圖1 旋轉編碼器提供電機軸的方向、位置、速度和加速資訊。 |
編碼器可以建基於各種技術,所有這些技術都可提供標準的A和B正交訊號數位輸出,某些型號還可提供索引輸出(圖2)。
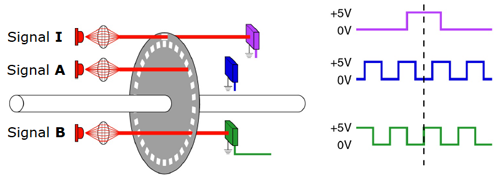 |
圖2 光學編碼器的標準A和B正交訊號及索引訊號 |
換向編碼器還提供U、V和W換向-相位通道輸出(Commutation-phase Channel Output),如圖3所示。
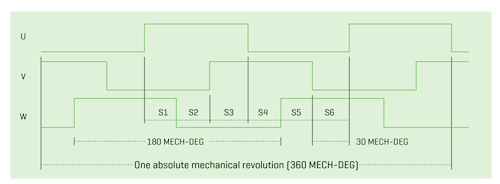 |
圖3 換向編碼器所產生的U、V和W波形 |
三類編碼器各據山頭
光學技術、磁技術或電容技術是最為人所熟知的三種編碼器方法。簡單來說,光學技術採用開槽(Slotted)圓盤,一側是發光二極體(LED),而光電晶體則在對面的另一側。當圓盤轉動時,光程被阻斷,所產生的脈衝可指出軸的轉動和方向。雖然光學方法的成本低且效率高,但是會因為兩個因素而使得光學編碼器的可靠性下降。首先是污垢、灰塵和油脂等污染物會干擾光程,其次是LED的使用壽命有限,通常幾年內其亮度會損失過半,而最終會被燒壞。
除了利用磁場而非光束之外,磁編碼器的結構與光學編碼器類似。磁編碼器以磁片代替開槽的光輪(Optical Wheel),磁片會在一組磁抗(Magneto-resistive)感測器上轉動,而磁片的任何轉動都會在這些感測器中產生響應,然後會被傳送到訊號-調節前端電路,以確定軸的位置。雖然磁編碼器的耐用性較高,但是準確性不如光學編碼器,且容易受到由馬達產生的電磁干擾所影響。
第三種方法即電容式編碼方法,具有光學編碼器和磁編碼器的所有效益,但是卻沒有它們的缺點。這種技術所採用的原理與成熟、低成本但精密的數位游標卡尺(Vernier Caliper)相同。它具有兩組經過編排的柱或線,一組設在固定的元件上,另一組設在運動的元件上,形成有如發送器/接收器對的可變電容器的配置(圖4)。當編碼器轉動時,一個積分特定應用積體電路(Integral ASIC)會計算這些線的變化次數,並利用內插法尋找軸的位置和轉動方向,建立標準的正交輸出,以及由其他編碼器提供且用於控制無刷直流馬達的換向輸出。
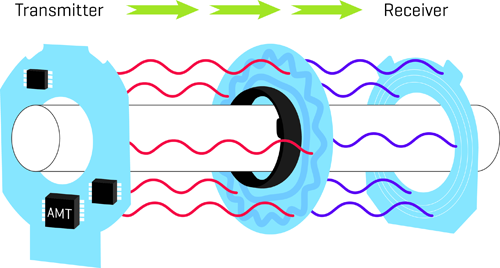 |
圖4 由與電機軸連接的轉子所發射之訊號,在調變後會產生脈衝,電容式編碼器計算這些所接收到的脈衝的數量。 |
這種電容式技術的優點是不會磨損,而且不受工業環境中常見的灰塵、污垢和油脂等污染物質的影響,使其在本質上比光學編碼器更可靠。電容式編碼器還具有數位控制特徵帶來的性能優勢,包括調節編碼器解析度的能力(脈衝/轉數),使用者毋須更換解析度更高或更低的編碼器。
電容式編碼器走向數位
舉例來說,CUI的AMT31系列就是一款先進電容式編碼器,可提供A和B正交訊號索引訊號,以及U、V和W換向-相位訊號。它有二十個介於48~4,096脈衝/轉(PPR)之間的可選遞增解析度,七個介於2~20之間的馬達極對(Motor Pole-pair)。此外,還具有便於安裝的鎖定轂(Locking Hub),以5伏特(V)電源軌操作,僅需16毫安培(mA)的供電電流。
電容式編碼器的效益不僅只是卓越的性能、靈活性及短期和長期穩定性。與光學和磁編碼器不同的是,電容式編碼器的數位輸出將系統設計帶進21世紀,從產品開發、安裝到維護的各個編碼器使用階段中,提供許多獨特的系統效益。
究其原因,是因為光學或磁編碼器的輸出僅能夠應付需要,但不具備「智慧」,無法為用戶提供靈活性、見解(Insight)或操作上的優勢。相較之下,電容式編碼器是數位式的,並且利用內建的ASIC和微控制器來提供其他的特點和增強性能。這種智慧輸出在許多方面都會改變使用者和性能的形勢,同時還與標準編碼器輸出百分之百相容。
邁向數位化 編碼器功能漸趨多元
仔細看看AMT31系列等電容式編碼器中的ASIC和微控制器所能實現的更多優勢。首先,其電容式編碼器的數位特性可以實現簡單、快速的One Touch歸零。這個過程非常簡單,激勵適當的馬達相位便可以將馬達軸鎖定在預定的位置,並且命令編碼器在這個位置歸零,所需的全部時間僅1至2分鐘,並且不需要特殊的儀器。
相反地,利用光學或磁編碼器以機械方式將換向訊號與馬達繞組對位歸零,是一個步驟繁多、複雜和經常令人沮喪的過程。它需要鎖定轉子,進行物理對位,以及後向驅動(Back-driving)馬達,同時使用示波器來觀察後部電磁場(EMF)和編碼器波形,以便實現正確的零交叉對位。這通常是一反覆進行的過程,為了微調和驗證,許多步驟都需要不斷地重複,所以整個過程可能會用掉15至20分鐘。
其次,AMT系列的數位特性還可大幅改善系統設計的過程,提供靈活性和診斷功能,並且實現馬達和馬達-控制器性能的評量。特別地,由於單一電容式編碼器能夠支援廣泛的解析度和極對數值(Pole-pair Value)範圍,因此設計人員能夠使用這種可程式設計解析度的功能,在控制器和演算法開發期間動態地調整比例-積分-微分(PID)控制迴路的回應和性能,而無須購買和安裝全新的編碼器。
該系列中內建的智慧功能還可以進行板載診斷,從而加快現場故障的分析。編碼器可以接受查詢,以表明它是否運作正常,或者是否有由於軸的機械錯位(Misalignment)或其他問題所造成的某種故障;因此設計人員可以很快地確定編碼器有否故障及找尋問題的來源,從而排除編碼器本身可能存在的問題。而且,工程師也可以使用這項功能作為預防性的措施,例如在運行程式之前執行測試序列以確定編碼器狀況良好。這些功能可以讓設計人員將停機時間(Downtime)減至最少,同時預見裝置在現場使用時可能出現的問題,但光學或機械編碼器並未提供。
此外,數位介面還可以簡化材料清單(BOM)。由於編碼器可以根據所需的特定變化(PPR、極對以及轉換方向)以軟體來量身打造,所以不需要為多馬達的產品(Multi-motor Product)、多種產品或安裝地點列出及儲存不同版本的部件材料。
智慧編碼器結合GUI 客製化非難事
用於電容式編碼器而且建基於Windows個人電腦(PC)的AMT Viewpoint軟體則可以加快開發的速度,並且只需簡單的操作便能夠完成確認型號和型款等耗費時間的繁瑣工作。它只需要一根通用序列匯流排(USB)纜線來與編碼器介接,並且實施簡單的串列資料格式。
此外,其圖形使用者介面(GUI)讓使用者可以根據應用的需求來量身打造和客製化其所需的編碼器(圖5)。
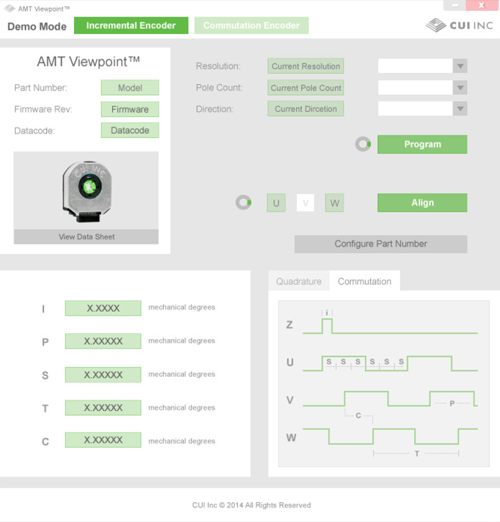 |
圖5 AMT Viewpoint軟體提供易於使用的開發介面 |
而其設定螢幕可讓使用者檢視關鍵的編碼器波形和定時,並且會隨著編碼器選項的改變而自動調節。透過圖形使用者介面程式設計編碼器僅僅需要幾個按鍵,每個週期大約需要30秒即可完成。最值得注意的是,編碼器針對A、B、索引或換向模式的對準或歸零僅僅需數秒的時間,這與使用非可程式設計編碼器來完成這項工作的長時間形成鮮明的對比。
在展示模式,使用者能夠使用圖形使用者介面以及執行編碼器相關的運作,就像連接著實際的編碼器一樣;這是一種便利的方法,可讓使用者在購買或實際使用之前即可熟悉編碼器和工具。圖形使用者介面還可針對特定的編碼器版本產生可訂購的(Orderable)元件編號,其中包括輸出格式、套(孔)適配器以及安裝基座等選項。
編碼器新變革 未來發展可期
建基於電容式技術之編碼器的優勢,不僅只是提供更佳的性能和可靠性,例如可提供智慧功能以支援可程式設計設置和安裝特性,實現運作智慧化並且簡化存貨管理。當這些特性與建基於個人電腦的圖形使用者介面相結合,能夠提供易於使用的先進功能,大幅地簡化編碼器在所有方面的使用,從樣品設計、評估和除錯,直至安裝和配置,以及診斷和存貨的最小化。雖然這種編碼器具備所有這些功能,但其成本只相當於其他編碼器,還可維持與標準輸出類型和格式的相容性,同時實現較低的功耗。
(本文作者任職於CUI)