2014年的消費性電子產業,最熱門的焦點仍然在於智慧型手機、平板電腦等智慧手持裝置產品。各家品牌業者除致力提高手持裝置的各項性能整合和軟硬體規格外,亦積極迎合中低價市場快速成長的發展趨勢。
手持裝置市場 朝平價高規發展
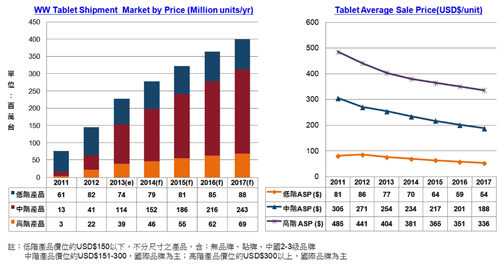 |
圖1 全球平板電腦銷量區隔分布(圖左)及不同區隔平均銷售價格年度變化(圖右) |
以2013年產品單價在300美元以下的中低階平板電腦產品來說,銷售數量占整體市場規模83%,另外在產品的平均銷售價格(ASP)表現上,即便是高階機種的平均銷售價格也呈現逐年下跌的情形(圖1)。此種中低價位機種當道、產品單價下跌的情形,也影響了各項零組件的市場銷售與技術發展。
做為智慧手持裝置中能量主要來源與電力儲存媒介的電池,同樣也受到平價高規需求趨勢的影響,設計者除了導入更高能量儲存效率的電池技術外,也必須要兼顧零組件的成本控管要求。因此對於電池供應商來說,除了以提高電池性能做為維持銷售獲利的策略外,也須要思考將產品成本降低的技術發展可能性,來兼顧並維持與下游智慧手持裝置品牌業者的供應關係。
電池需求特性 朝四大方向發展
電池需求特性發展,可以從直觀增加電池電容量、提升電池能量密度、元件功能整合,以及導入低成本材料等四大方向來加以說明。
直觀增加電池電容量
手持裝置的電池技術近年在大量的運算功能需求、螢幕尺寸增加、支援多種高速傳輸技術的多重要求影響下,電量消耗速率快速增加,但是在電池技術的發展上,實在無法跟上此種幾何倍數成長的消耗速度,因此手持裝置設計者與電池供應廠商,面對產品使用續航力提升的技術問題,最直觀的解決方法就是在設計時提升電池電容量做為首要解決之道。
如觀察智慧型手機兩大品牌廠商三星(Samsung)Galaxy S系列產品和蘋果(Apple)iPhone產品過去3年的電池規格演進,Galaxy S搭配的電池由第一代的1,500mAh電容量,成長到2013年新款Galaxy S4的2,600mAh,3年時間下搭配的電池電容量成長73%;而蘋果在2012年推出的iPhone 4系列智慧型手機使用1,440mAh容量鋰電池,到2013年時的高階iPhone 5版也提升電容量至1,560mAh。
在電池電容量提升的設計變化上,產品設計者與電池供應廠商可以藉由增加整機結構內電池體積,或是提高電池能量密度的兩種思維發展,考量到輕薄化的手持裝置外觀要求,設計者若必須選擇將電池體積適度增加,大多是在長寬尺寸比例上進行擴增,而較少更動電池厚度尺寸,甚至希望採用厚度更低的電池規格。
提升電池能量密度
增加電池體積重量的做法,較不符合可攜式電子產品朝向輕薄化的產品設計趨勢,也變相排擠其他零組件的應用空間,因此當電池體積因產品設計無法擴充時,必須以提升電池能量密度的做法來思考,而其中又可分為由材料著手,以及改進電池製造技術兩種做法。由材料著手主要是直接更換高能量的材料體系,包括高能量/高電壓正極材料與高能量負極材料,以及減少非活性物質在電池當中所占體積等;在改進製造技術上,主要以提升極板壓實密度為主要重點。
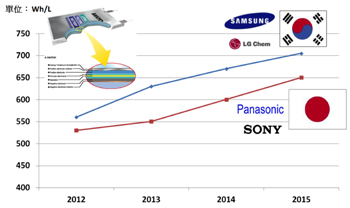 |
圖2 日韓電池生產領導廠商電池芯能量密度技術Roadmap |
以圖2日韓兩大國際領導廠商在智慧手持裝置應用之軟包裝鋰電池能量密度未來發展規畫來看,韓系電池廠商是將體積能量密度提升做為重點技術發展,所銷售的電池在2013年已可達到超過600Wh/L之水準;日系業者在電池技術上採取穩步發展策略,在其對顧客呈現的未來技術藍圖中,能量密度提升的步伐較為謹慎。日韓兩國的主要發展廠商均將高能量/高電壓材料做為主要核心技術應用,也影響了更上游的電池材料產業需求走向。
提升電池電容量與提升電池能量密度的做法,皆符合手持裝置平價高規需求的發展。電池廠商可以選擇將同規格的電池致力於降低其生產成本與出貨價格來符合平價化要求;但也可以選擇將電容量以及電池能量密度提升,來保持電池的出貨價格穩定,維持毛利率與附加價值,也更能使其下游顧客顧及平價高規這兩端看似有所衝突的發展路徑。
元件功能整合
另一種受到平價高規需求趨勢影響的電池技術發展,主要是在電池/電源控制元件的整合趨勢上,手持裝置廠商致力於各項不同運算IC功能整合,除以更少的晶片與更低耗能的運算元件來節省電力外,也希望在電池管理系統或電源管理IC上從事整合工作,如處理電池電壓監控、計算、穩壓、電量計算、充放電行為管理等工作。
近年來,晶片商陸續將電壓調節器、監控器與電壓控制器整合在同一電源管理IC上,除了可幫助延長電池的使用時間外,還兼具電源保護、電壓管理等功能。因此將各項功能元件整合單晶化以縮小體積,是各家廠商一致的目標,如目前行動電話製造商都朝向將保護IC、充放電電路、電源管理IC等周邊電路封裝成單一晶片應用,再與邏輯IC構成雙晶片的晶片組。
過去,在行動裝置的電源設計上,最低價的做法是分別將保護IC和功率金屬氧化物半導體場效電晶體(Power MOSFET)封裝為兩顆不同元件;另外部分廠商選擇將保護IC與Power MOSFET放入同一封裝成為多晶片封裝(Multi Chip Package, MCP)方案,以韓系廠商應用較為積極;但在近年因韓系智慧型手機業務大幅成長,連帶使其慣用之整合保護IC及MOSFET之電池保護電路解決方案市場滲透率有所提升。
至於再進一步整合保護IC、Power MOSFET和印刷電路板(PCB)的晶片直接封裝(Chip on Board, COB)的做法,也因可進一步再降低所占空間和整合元件,雖然單價上目前仍高,但已漸成為主要解決方案之一。
導入低成本材料
要讓電池成本進一步有所降低,導入低價材料是主要思考方向之一。近年在導入低價材料的做法上,最顯著的例子是日韓電池廠對於材料採購策略的轉變,過去以日系電池材料廠商做為產業主要供應者的特色已有所改變,包含Panasonic、索尼(Sony)、Hitachi Maxell,以及韓系三星SDI(Samsung SDI)、樂金化學(LG Chem)等大廠,近年除了將產線陸續遷移至鄰近下游組裝產業的中國大陸以減少運輸成本就近供應外,也就近尋求與中國大陸電池材料廠商的採購合作,在維持電池性能和安全性的前提下,致力於尋找可供應低價材料的廠商。
到2012年底為止,針對日韓兩國電池廠商的上游材料供應鏈分析時,供應較低價材料的中國大陸材料廠已占近半之供應比重,也成為電池廠商降低電池成本、符合平價化需求趨勢的另一種途徑。
平價高規需求下 技術發展思維丕變
鋰電池的生產與產品開發,為了符合平價高規的需求特性,並不能僅考量單一指標的改良,還必須有一定的安全性、循環壽命以及材料本身的結構穩定性等要求。要使電池朝向高電容量發展,原則上可考量選擇體積能量密度更高的材料體系應用,如鋰鎳錳鈷三元系材料(LiNi1/3Mn1/3Co1/3O2)或鋰鎳氧化物(LiNiO2)做為正極材料選項,可在其他材料/生產條件不變下,提高13~35%的電池能量密度。
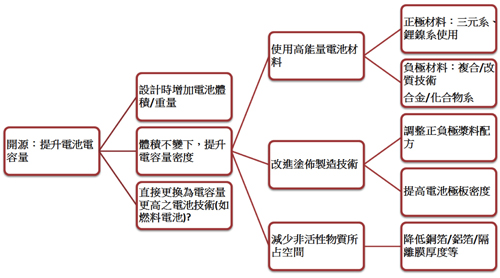 |
圖3 提升電池電容量密度為主要考量的技術發展途徑 |
非碳系負極材料近年來主要以化合物與合金兩種開發方向為主流,此兩系材料比起現有碳系材料來說,能夠吸納更多的鋰離子,應用在電池上的電容量、充放電循環性能改善效果均為碳系所不及。另一種做法是藉由生產程序的控制增加極板密度,以Panasonic高容量鋰電池芯設計的概念為例,除了前述所提的更換正極材料與負極材料、提高塗布厚度做法外,也將極板體積密度提升8%,換言之,同樣的體積當中含有更多的活性物質,此種做法即為應用製程技術來提高極板密度和電容量的技術發展思維(圖3)。
要讓電池的成本降低,主要可由導入低價化材料、提高製造良率與標準化/規模化生產著手。導入低價材料的思考可以進一步細分為找尋相同材料體系的低價方案選擇,前述所提及的日韓電池廠採購轉向中國大陸的狀況即為此類;另一種方式則是直接選擇使用更低價的材料體系,如由過去使用的鋰鈷氧化物(LiCoO2)正極材料轉向使用鋰鈷鎳錳三元系材料;負極由過去的人造石墨,改為低價的改質天然石墨等。
在提高製造良率的工作上,由於良率提升可直接讓生產成本下降,因此廠商多考量提高生產自動化程度,改進製程與生產設備的技術來提高良率;或是採用過往累積生產經驗較為豐富的材料/生產體系來做為公司經營主軸。
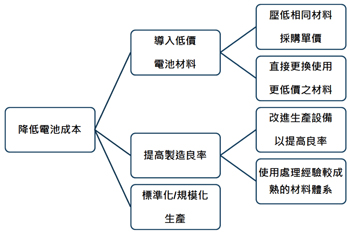 |
圖4 降低電池成本為主要考量的技術發展途徑 |
另外,由於大規模生產也有一定的生產規模經濟效益(圖4),因此也可以做為降低電池成本的另一做法,這也是在電池產業產能供過於求的現況下,國際大廠仍然持續投入新設備而不傾向於減產的另一主因。
既然平價化、高規格化的發展方向勢必是今年的手持裝置產品下游需求趨勢,朝向多重功能整合入單一裝置,同時要求產品使用續航力的需求大趨勢也可望持續,未來在電子產品設計時,所須搭配之電池電容量必定日漸增加,前述所提之各項提升鋰電池電容量的做法與研究也會在未來持續被討論。
朝平價/高規/安全三軸向發展
近年因應輕薄化、美觀等電子產品設計趨勢,內建不可抽換電池的設計也逐漸增加,電池耗盡時,終端消費者無法以關機抽換電池的方式維持續航力時,因此內建於電子產品中的電池性能,以及內建電池的電容量所代表的產品使用續航力就更加重要。
雖然電容量提升的電池技術趨勢十分明確,但是去年美韓兩大智慧型手機大廠分別都出現電池故障與爆炸的多項個案,手持裝置廠商除蒙受財務與產品回收的商譽損失外,包含電池廠也承受極大的社會壓力,因此電池廠商仍然必須針對電池各項性能指標進行通盤的評估,不能因為妄圖電容量的提升,就過度降低其他重要性能指標的表現。
其中,尤其在電池安全性上,向來為鋰電池產品重點,在更換高能量正極材料時可能衍生的安全性影響,以及在更換合金/化合物負極材料時衍生之體積膨脹率過高導致的電池結構破壞,甚至造成短路爆炸等問題也都必須要一併考量。
為進一步提升電池品質,預料今年電池供應商會將去年的電池品質/技術問題視為警鐘,做為今年電池技術設計評估時納入考量的重點。
(本文作者任職於工研院IEK)