近年來,隨著數位影像模組技術不斷地進步,使得人類對於影像的定義和應用有了不同以往的認知。數位化後的影像更利於傳輸、分享及儲存,並且可以不受限於時間與空間,迅速且真實地將影像傳送至世界的每一個角落。
在這一波影像的革命風潮中,最惹人注目的當屬影像感測模組的普及化,可針對不同的用途和類型的產品搭載相應的影像感測模組,例如類似行動電話、筆記型電腦等在體積大小有一定限制的電子機器,即可搭載小型化、低價化的影像感測模組。以往,如電荷耦合元件(CCD)影像感測模組或互補式金屬氧化半導體(CMOS)影像感測模組,其架構大多具備鏡頭、機構件、及影像感測器這幾個重要元件。而其組裝生產都倚賴人工居多,因此在產品成本控制上有一定的瓶頸。由於影像感測模組應用於消費性電子產品漸往小型化、低價化發展,讓各家業者更積極尋求下世代影像感測模組的生產技術。
自2001年開始,許多業者嘗試利用半導體製程、立體電路構裝等技術去縮小模組體積以及自動化生產影像感測模組,並於近年來逐一開花結果。
小型化/低價化擴大市場利基
在日常生活中,影像感測模組幾乎處處可見,例如照相手機、搭載網路攝影機的筆記型電腦、戶外大量使用的安防監控攝影機,以及倒車或車行中所使用的車用影像系統等。而影像感測模組普遍化的主要原因,除了消費者對於影像的需求更甚以往之外,價格的降低是最主要的原因。以VGA影像感測模組為例,2002年,VGA(640×480畫素)影像感測模組的價格在10美元以上,而目前僅需1.8~2美元,也就是說,可用5年前的四分之一價格買到VGA影像感測模組(圖1)。
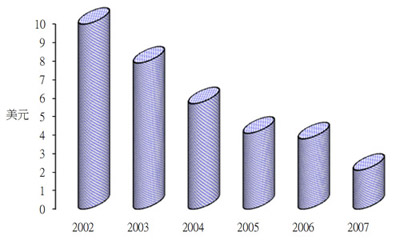 |
資料來源:日經(02/2008) 圖1 2002~2007 VGA影像感測模組價格趨勢 |
倘若影像感測模組的價格能夠進一步壓低,相信該產品的應用市場可以進一步地拓展,尤其是中國、巴西、非洲等新興國家市場對於各類型的消費型電子產品的需求力道相當強勁。就照相手機來說,若影像感測模組能夠以更低的成本搭載於低價手機上然後大量行銷,估計2010年的照相手機市場規模將達到10億支以上。
光學元件整合與製程技術開發成關鍵
目前,影像感測器已囊括大部分的半導體產品市場(圖2),原因是影像感測器應用於消費性電子產品的情況日益增多,如數位相機等產品。而晶圓級封裝(Wafer Level Packages, WLP)相機(Camera)是由半導體製程技術中所衍生出來應用於整合影像感測和光學元件的製程技術。利用晶圓封裝技術來自動生產晶圓級影像感測模組,就可以像製造電子零組件一樣大量且自動化製造,達到低價化的目的。
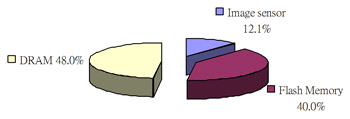 |
資料來源:Semiconductor Today(01/2007) 圖2 半導體各類產品於2006年市場實績比重 |
首先來了解一下WLP Camera的製作流程。傳統影像感測模組是由三大部分元件所組成:光學感測器、光學元件和相關機構夾持、數位訊號處理器(DSP)元件(圖3)。而晶圓級影像感測器模組,當然也將是由這三大部分元件來組成。首先將DSP電路及利用深蝕刻技術製作而成的微光學元件夾持機構建立於晶圓上,再將多層堆疊而成的光學鏡頭玻璃晶圓片與其結合,成為光學鏡頭加上DSP電路所組成的晶圓堆疊模組。接著在影像感測器晶圓上再做光學品質校正(以上所描述的單位都是數以千計),等到一起校正完了之後,再一併過錫爐(Reflow Process)固定焊腳,然後切割出一顆顆完整的影像感測器模組(圖4)。
 |
資料來源:PIDA 圖3 影像感測器模組架構 |
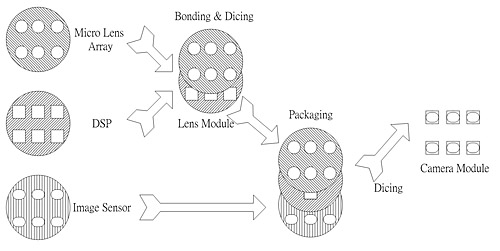 |
資料來源:PIDA (02/2008) 圖4 晶圓級封裝相機製程 |
製作過程中牽扯到的技術,包含半導體微影、蝕刻、雷射切割晶圓或是光軸調整等技術,都是相當複雜而先進的,而其中最關鍵的技術就屬微光學元件製造及過銲錫爐的高溫對於模組材料的影響。由於塑膠鏡頭無法承受焊錫爐的高溫,所以必須以玻璃製造能夠耐高溫錫爐的微光學元件來組成鏡頭組。為了排除這樣的難題,Tessera和Schott等廠商已發展出各自的解決方案,Tessera開發出OptiML WLC技術,而Schott研發opto-WLP技術。
大體說來,這些新技術主要都是利用玻璃耐熱性佳的特性,來製作能夠對應錫膏溶焊高溫的薄形圓板(光學晶圓),並採用與半導體製程相同的晶圓製程(Wafer Process),以蝕刻微影曝光的方式,同時做出數以千計的微光學元件。而構成微光學元件的玻璃晶圓片數以及各晶圓的鏡頭設計是取決於影像模組之規格要求,當在各晶圓的表面上形成鏡頭模組之後,將之與感測器晶圓作精準的對位堆疊,如此一來,便可形成數千個影像模組。
以晶圓級封裝技術來大幅改變傳統影像感測器的製作模式,優點不勝枚舉。原因在於,晶圓級封裝技術原本是為了在電子元件上構築立體電路來達成體積和重量微小化,以便在同樣面積的晶圓上生產更高比例的元件。而當這樣的理念應用於生產影像感測器時,就是期望能夠將影像感測器生產轉化成電子元件產業一樣,進而標準化和大量生產。
利用晶圓級製造技術的第一個優點是生產成本低廉。光學元件的尺寸如果能夠縮小,平均每片晶圓的元件數量就能增加,而每片微光學元件的製造成本也可以降低,再配合感測器或DSP的小型化,且光學元件也能小型化時,單位晶圓生產成本便能大幅降低,而影像模組的小型化與低成本化,正是推動晶圓級生產技術的原動力。另一個優點是可生產自動化。鏡頭模組晶圓與影像感測器晶圓經過一次性的光軸對焦,直接堆疊黏著固定,免除了傳統需要人工手動方式對焦再黏合的步驟,並且可以自動化生產。另一方面,也可以藉由自動化對焦調整來提高生產良率。第三個優點則是影像感測器模組電子元件表面黏著技術(SMT)生產。由於微光學元件材料是玻璃,可以耐受過錫爐的高溫,因此可以將生產完成的影像感測模組藉由過錫爐直接焊接於基板上,直接整合於一體化的電子製程,在整體製程上達到省料低成本的目標。
廠商垂直整合勢在必行
一直以來,系統廠對於影像感測模組類的產品都會要求模組廠商和光學鏡頭廠必須達到低成本化及小型化的要求,以便讓影像模組搭載率大量普及。而事實上,當普及率大幅提升時,系統廠已將搭載影像感測模組視為標準配備,更希望影像感測模組能夠循電子元件生產模式般大量且自動化生產。
這股需求的聲音傳到影像感測器廠的耳中,自然是商機無限,於是開始開發運用晶圓級封裝技術,以達到影像感測模組的低成本化、過錫爐生產整合和生產自動化。當影像模組市場持續快速成長下,所面臨的成本下降壓力將更大。以往光學鏡頭廠對影像感測器模組廠商的成本要求,往往難以配合,因為組裝鏡頭需要大量人工。而對模組廠來說,由於成本壓力,垂直整合供應鏈將是達成影像感測模組的必要手段。能夠自動化生產且單位生產量大的晶圓級影像感測器生產技術,才能受到模組廠和影像感測器廠的青睞。
以Tessera為例,Tessera雖然以封裝廠起家,但是著眼於上述的趨勢,已開始進行技術開發和購併擁有其他技術的公司,如購併了專精於表面黏著技術與晶圓級封裝技術的Schellcase、長於微光學元件製作技術的Digital Optics,以及專擅於數位調焦技術的Eyesquard(圖5)。如今,Tessera已正式提出OptiML WLC,大力提倡晶圓級封裝影像感測器技術,希望能夠改變傳統影像感測器模組的生產模式,並期盼藉著影像感測器模組低價化,能夠開創出更普及的應用。
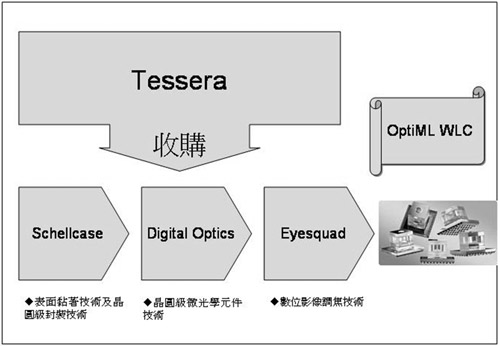 |
資料來源:Tessera(PIDA整理) 圖5 Tessera公司動態 |
目前晶圓級影像感測模組能夠推展到市場上的只有VGA等級的影像感測器模組,而市場上對於該項產品仍有疑慮,其中光學品質更受到傳統光學廠的莫大質疑。但是,在影像感測器廠大力推動光學元件電子化生產之下,傳統光學廠除了證明傳統光學元件組裝和設計模式是影像品質的最佳解決方案之外,其生產方式可能得花費更多的心力於半自動組裝生產或全自動生產開發上,傳統人力大軍的生產模式在數位影像時代肯定會面臨更嚴苛的挑戰。